In the last few years and as the result of international and regional laws and strategies to reduce global gas emissions, Liquefied Natural Gas (LNG) has been increasingly adopted as an alternative fuel for shipping.
While the adoption of LNG as an alternative marine fuel offers somemajor environmental and economic benefits, it also poses some challenges. These include the potential risks of methane leakage across the LNG supply chain; the capital investment required for equipment for cryogenic environments; safety concerns; and the still-developing LNG bunkering infrastructure.
For these reasons and more, and in order to promote the more widespread and safe usage of LNG as an alternative marine fuel, all stakeholders need to be involved in the development process of LNG fueled vessels and bunkering operations. This is where we, at HABONIM, come into the picture. As one of those stakeholders, we understand how much effort goes into the planning of every single component in cryogenic infrastructures. In this blog post, we will be focusing specifically on the criteria that need to be considered when selecting valves for LNG bunkering applications.
Criteria for selecting LNG valves
LNG bunkering can be defined as the provision of LNG to be used as a fuel for the propulsion of LNG-fueled waterborne vessels and/or for energy on board the vessels while they are at berth. It involves the transfer of LNG fuel from a specific distribution source to an LNG-fueled ship through a value chain that differs per application and use case. In addition, bunker ships and bunkering infrastructure is increasingly used for fueling and supplying land-based fueling stations, trucks, and inland shore infrastructures.
As LNG bunkering applications are usually characterized by multiple stakeholders and complex regulatory contexts, and this makes the selection of equipment (including valves) for these operations somewhat challenging.
Four main valve technologies can be used in cryogenic applications such as LNG bunkering: globe valves, floating ball valves (top-entry and side-entry), trunnion ball valves, and top-entry trunnion ball valves. Each of these technologies offers specific benefits for different applications. For example, HABONIM’s top-entry trunnion ball valves are ideal for cryogenic applications in harsh environmental conditions. However, side-entry ball valve technology which is also suitable for cryogenic applications can be more cost effective in calmer environmental conditions. While most project specifications call for the use of top-entry valve technology in cryogenic applications, this is not always actually required.
For this reason, we focus on helping our customers to carefully analyze their project requirements and the specific
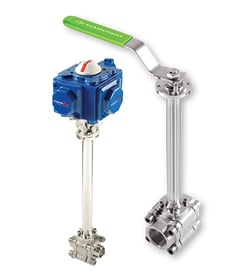
system needs in order to offer them the best and most cost-effective combination of valves for their specific application and regulations. This approach can lead to a significant reduction in the overall project cost and have an even more significant effect on the life-cycle cost (LCC) of the ship or facility, without compromising on performance and safety. This analysis is based on the following criteria:
1. Type of LNG Valves installation
When selecting valves for LNG bunkering installations, it’s important to consider the type of installation, which include:
- LNG import terminals and bunkering facilities – these stationary facilities offer LNG services such as reloading, the transfer of LNG from one vessel to another vessel, and the loading of LNG bunkering ships.
- LNG bunkering ships – supply LNG directly to LNG-fueled ships or to LNG bunkering facilities where LNG is stored for other vessels.
- LNG inland and onshore facilities – supply or refueling with LNG to or from onshore fueling facilities, tracks, storage spaces, and more.
The type and size of the LNG bunkering vessel has a significant impact on the type of valves required. For example, in the case of small LNG bunkering vessels used to directly supply LNG to ships inside or outside a port as well as to inland onshore facilities, specific considerations need to be taken into account. These include the fact that small-scale LNG operations (SSLNG) need to be small and lightweight and still maintain maximum flow for shorter loads and offload operations; that they need to meet stringent inland transportation regulations, and deal with multiple municipal authorities.
With a proven track record in LNG and advanced SSLNG projects, HABONIM has the experience to guide companies in selecting the best valves for their specific LNG bunkering applications. For example, HABONIM was selected by Titan LNG as a supplier for the FlexFueler001, the first inland bunker pontoon in Europe designed to supply LNG to inland waterway ships from a fixed location or to be navigated to supply larger seagoing vessels with LNG while they load or unload their cargo. This involved a long and complex design process that included the selection and testing of valves to ensure they meet the stringent requirements for zero fugitive losses and inline leakage tightness, and fire-safe and cryogenic usage.
2. Location of LNG bunkering installations and environmental conditions
LNG bunkering installations, which include both stationary facilities and moving vessels, can be located in multiple sites such as ports, offshore, in open seas, and in inland waterways. This, as well as the climate and other geographical characteristics, affect the design and selection of valves for the installation. For example, seagoing vessels are exposed to harsh conditions such as high waves, stormy weather, and wind. These factors apply mechanical stress to the vessel structure and to piping and equipment installed on it, which results in high structural deflections and possible leakages through the piping and valve body joints. In these cases, top-entry ball valves are required as they can withstand these harsh conditions. This is because the valve body is made of a single piece welded to the piping, with no bolted joints in body construction that might be compromised by these deflections, and potentially cause methane release to the atmosphere.
In the case of port-operated vessels, this depends on the level of port protection from sea waves, whether the vessel is always stationary or also needs to travel in open seas occasionally, possible future relocation to less protected ports, and more. These conditions affect the selection of valves, as side-entry valves are sufficient for calmer environmental conditions and top-entry valves are required for vessels exposed to high body deflection as a result of harsher environmental conditions. For example, for vessels located in inland waterways, there is usually a reduced need for more expensive top-entry valve technology as the potential for stormy environmental conditions that result in vessel deflection is lower. In these cases, top-entry valves can be combined with side-entry valves with enhanced double-sealed body construction and ISO 15484-1 certified stem sealing (Total Hermetix).
3. Budget
As LNG systems are designed and built to serve in small-scale bunkering operations where cost considerations are becoming more significant, budgetary restrictions form the framework for system design and valve selection. In the case of LNG bunkering applications, it can be extremely challenging to find the right balance between meeting budget requirements, meeting stringent standards, ensuring long-term performance, and ensuring safety. For this reason, it’s important to consider all of the abovementioned factors, together with suppliers, in order to find the right combination of valves that enable project integrators to answer all requirements.
4. Regulations, guidelines and standards
LNG bunkering operations are governed by stringent regional and international standards, regulations, and guidelines that aim to ensure maritime safety and security, and prevent potential pollution or environmental damage caused by natural gas installations.
These include:
- The highest regulatory level codes, such as IGF and IGC for LNG-fueled ships and LNG carrying cargoes, PED 2014/10/EU and TPED 2010/35/EU for pressure equipment and its transportation, IECEx and ATEX for explosive environments, and more.
- Industrial standards for cryogenic valves construction and testing such as BS 6364, EN 1626, MSS SP-134-2012, EN 12567; and for fire testing and design such as API 607 and ISO 10497.
- Classification rules and guidelines from well-known maritime classification bodies such as Bureau Veritas, DNV-GL, ABS, and others.
- This also affects the specific valve features required for cryogenic applications. For example, the need for Emergency Shutdown (ESD) to enable a safe and effective shutdown of LNG transfer in the event of an emergency, and a very high level of external and internal tightness of the valve or a double walled vacuum piping insulation to prevent excessive evaporation of the LNG during the filling and bunkering and to trace external leakages
It can be challenging to decipher these regulatory instruments, and for this reason, one of the most important components in LNG bunkering system design is the selection of product suppliers, as they can help navigate the ins-and-outs of compliancy and have the capabilities and expertise to meet the required standards.
Helping you navigate the requirements for LNG bunkering
At HABONIM, we believe in finding the perfect fit for every customer, every project, and every application. We hope that this guide has helped you understand the factors that need to be considered when selecting valves for your LNG bunkering application. Contact us if you have any additional questions.